(vervolg op Factory Digital Twin – Deel 2: Waarom is een Factory Digital Twin belangrijk?)
Om met succes een factory digital twin in hun fabriek te implementeren, zijn wheyco – een producent van wei-eiwitten – en Axians drie jaar geleden een reis gestart. Het idee achter de factory digital twin kwam tot leven toen CEO Marcel Boon contact opnam met Axians voor hulp om meer te doen met data. De operators moesten beter ondersteund worden bij het nemen van beslissingen gebaseerd op harde data. Businesswise zou dit noodzakelijk zijn om de productiedoelstelling, 20% meer output, te bereiken.
Inzicht verkrijgen
Samen met operators en planners dook Axians in de fabrieksprocessen en ondersteunende informatiesystemen, waarbij ze de volwassenheid van datalogging van apparatuur en de datarecords in verschillende informatiesystemen beoordeelden. Ook werden de standaard werkwijzen geanalyseerd om beter te begrijpen waarom er afwijkingen van de wekelijkse productieplanning optraden. Deze inzichten leverden een lijst op met requirements voor een betere productieplanning, die near realtime met de operators in de fabriek moest worden gedeeld.
Data Platform en Plan versus Actual Dashboard
Het inzicht in requirements resulteerde in de opzet van een data platform waarin proces-, product- en planningsdata werden geïntegreerd, gevalideerd en onderhouden. Dit data platform borgde de hoge kwaliteit van betrouwbare data dat nodig was om een Plan versus Actual Dashboard te voeden. Dit dashboard toonde vervolgens wat er werkelijk gebeurde versus wat er volgens het plan had moeten gebeuren. Het dashboard werd elke 15 minuten voorzien van de meest actuele data en werd op een groot scherm in de centrale bedieningsruimte en op verschillende kantoor-PC’s getoond.
Significante afwijkingen konden snel worden besproken binnen operatorteams en met de afdeling planning. Belangrijke vragen die naar voren kwamen waren:
- “Hoe en wanneer kunnen we weer conform planning produceren?”,
- “Moeten we batches gaan verschuiven of kunnen we de productiesnelheid verhogen?”,
- “Wat zijn de risico’s als we een andere productieroute nemen?”,
- “Wat is het algemene (jaarlijkse) outputdoel dat risico loopt?”.
Simulatie als noodzakelijke stap voor een Factory Digital Twin
Een snel en bevredigend antwoord op bovenstaande vragen kon de planningsafdeling echter niet geven. Daarom was de volgende stap om te gaan voorspellen wat de wijzigingen van een planning teweeg zouden brengen. Hiervoor werden de besturingsregels vertaald naar planningslogica. In dit geval naar voorspellingsmodel gebaseerd op discrete differentiaalvergelijkingen. Op basis van dit model konden verschillende planningen worden doorgerekend en gesimuleerd. Door verschillende machine-instellingen, opslagcapaciteiten, productkwaliteiten en batchsequenties te simuleren, kon een realistischer en haalbaarder planningsvoorstel worden vrijgegeven. De planning werd vervolgens geupload naar het Plan versus Actual dashboard. En hiermee was stapsgewijs de factory digital twin tot leven gekomen.
Optimalisatie
De volgende vraag die niet kon worden beantwoord door de afdeling planning was: “Is dit nieuwe planningsvoorstel dan ook meteen de meest optimale planning?”
Omdat de planningsafdeling te maken had met een complex planningsprobleem – een zogenaamd non-linear mixed integer problem – werd besloten om de planningslogica te om te zetten in een optimalisatie-algoritme. Hierbij werd gekozen voor de zogenaamde MIDACO-solver die gebaseerd is op mierenkolonie-optimalisatieprincipes. De solver rekent alle mogelijke combinaties op zeer efficiënte en snelle manier uit en komt vervolgens met het meest optimale planningsvoorstel. Deze kon worden vergeleken en getoetst met het planningsvoorstel dat op de oude manier was gemaakt, waardoor direct de toegevoegde waarde inzichtelijk werd.
Closing the loop
De laatste stap zal nog moeten worden gezet. Het betreft het automatisch koppelen van de machine instellingen die bij het optimale planningsvoorstel horen aan het productiebesturingssysteem. wheyco zal er in eerste instantie voor kiezen om een handmatige actie ertussen te laten zitten: pas nadat productie het nieuwe planningsvoorstel heeft geaccordeerd en de operator op de knop heeft gedrukt, worden de settings overgenomen en doorgezet. Daarna kan er weer op het Plan versus Actual dashboard gemonitord worden of er afwijkingen ten opzichten van de optimale planning ontstaan.
Factory Knowlegde Hub
De kennis en best practices die uit de vele discussies naar voren kwamen en in logica werden vertaald, maakten van de factory digital twin het kenniscentrum voor continue verbetering en productieplanning.
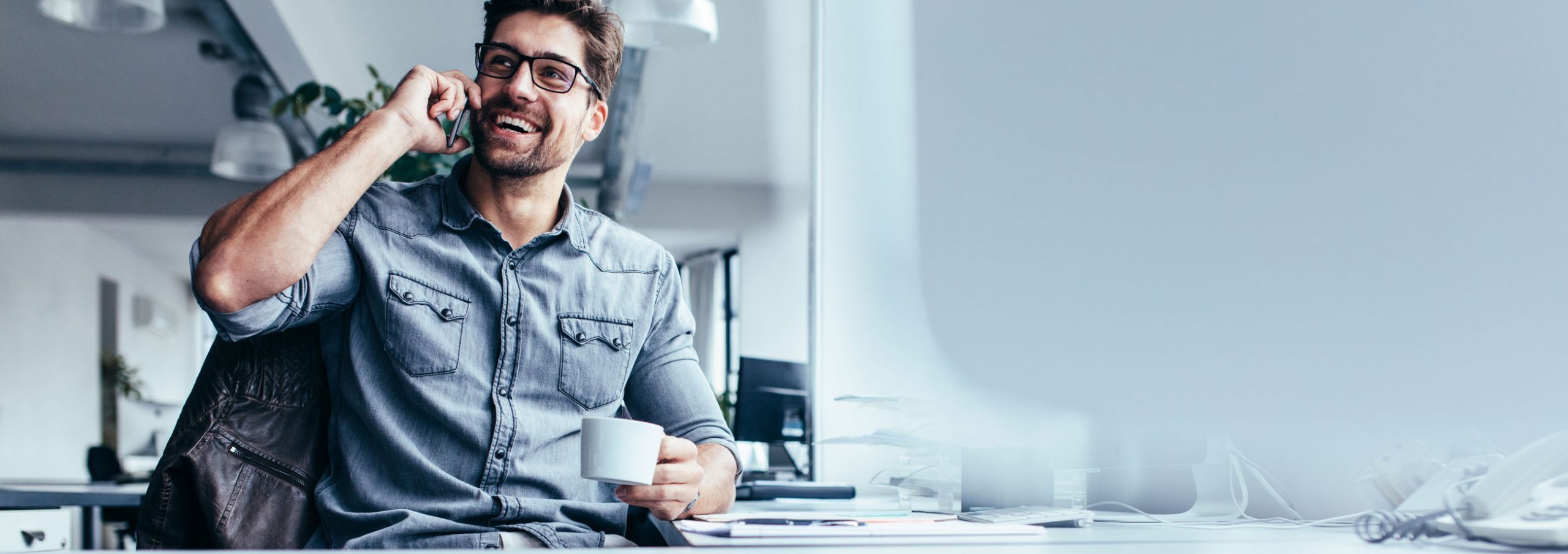
Hoe kunnen wij jou helpen?
Wil je meer weten over de digitalisering bij productiebedrijven? Wil je eens vrijblijvend van gedachten wisselen over jouw specifieke situatie? Vul onderstaand formulier in en dan nemen wij snel contact met je op.